Conquering Variability: A Key to Effective Project Work (Part 2)
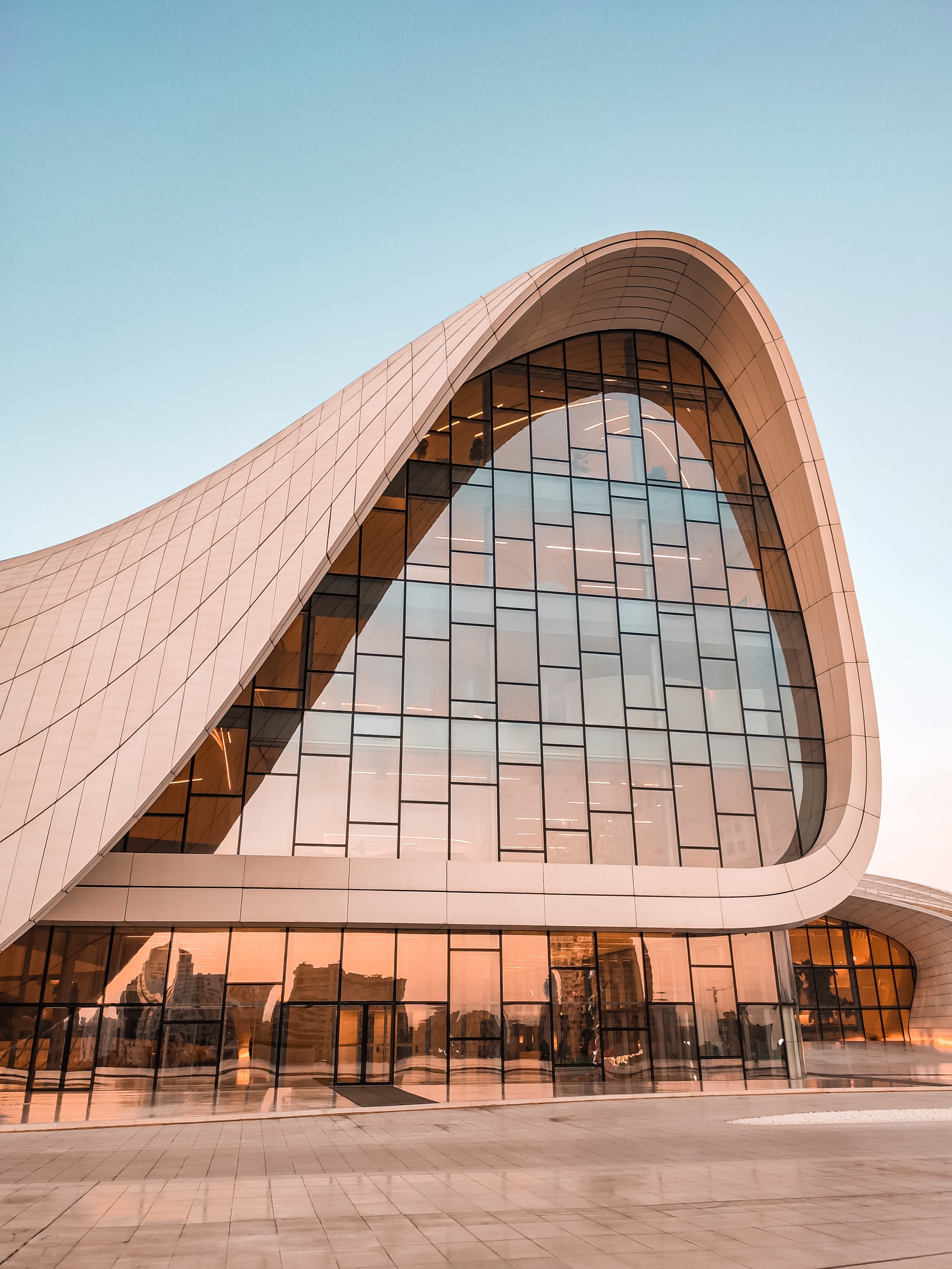
Conquering Variability: A Key to Effective Project Work (Part 2)
By Klaus Lemke
In my previous article, I presented the first part of a process for conquering variability. There I explained some simple ways to reduce the amount of variability that happens in design and construction processes. Experience tells us that we can usually eliminate a lot more unknowns and get typical work processes to settle down a lot more than you might expect. You can read that article here.
That said, this is still building — a world made up of one-off projects, short-term teams, and a whole host of surprises like unexpected weather, unsuitable soils conditions, and the discovery of a protected migratory bird or ancient burial ground on our site. Some variation is sure to be part of every design and construction project.
This leads me to the second part of conquering variability — dealing with the variability that remains. Here are three key practices that we’ve found most effective in dealing with these common challenges.
First, plan and execute work in small batches. Working in small batches does several things to help project work. It allows the work to be connected more tightly together, brings problems to the surface more quickly, and allows the team to respond much faster to unexpected changes. Think of it like this; If you divide the work into small pieces, you will never be far from the start or end of the current piece of work. The conclusion of the current work task provides an opportunity for the team to regroup, lick their wounds, and make a new plan before moving onto the next batch of work.
Next, include buffers that are visible, public, and shared by the entire project team. This one is about building team trust and learning to rely on each other when one member is in a jam. By making collective, visible buffers, you eliminate the need for each project participant to carry their own “secret” buffer to protect themselves against the unknown. Instead of say the roofer, framer, mason, and glazer each carrying their own 10-day schedule contingencies (a total of 40 days) the project can get by with say fewer than 20 days that each member can access if needed. This reduces the total schedule buffer that is required, and provides an opportunity for the team to work together to deal with any unforeseen events. The process provides a safety net while reducing unnecessary contingencies and providing transparency to the team about what is most important for project success.
Finally, make plans and decisions at the last responsible moment. This concept goes contrary to some traditional thinking about planning and decision-making. Yet, once you think about it, it makes perfect sense. Instead of making decisions as soon as possible, we are better off delaying until the moment just before the decision is actually needed. By delaying a decision, we can eliminate the second guessing that happens when we are forced to make decisions based on preliminary or incomplete information. Rather than changing our minds three times and leaving the team with confusion and frustration, we make the decision once with certainty and confidence.
The same concept applies to the creation of project schedules. Greg Howell once put it this way. “The further into the future we attempt to create detailed plans, the more wrong our plans will be.” Rather than creating a CPM schedule with thousands of activities at the start of a project, try focusing on the few important milestones that, if achieved, will guarantee the success of the project. Then, leave the detailed planning to just before that phase of work is set to begin. At that time, you will have more complete information, a more engaged team, and the full attention of the individuals who will actually execute the work. Only then can you make reliable plans that can actually be executed with confidence.
I have no illusions about a design and construction projects running as smoothly as a Toyota assembly line. It’s just a different world with different challenges, Yet, there is a lot we can do to conquer the unique challenges of this environment. Give some thought to reducing some of the variation that you have taken for granted in the past. You can do more than you think. Then design a process that tackles remaining variability head on, with transparency, collaboration, and lean thinking.
For more information about conquering variability, and how to put lean thinking to work in your projects, check out the book, Better Building: Lean Practice for the Project-Driven Organization.
Conquering Variability: A Key to Effective Project Work (Part 2)
By Klaus Lemke
In my previous article, I presented the first part of a process for conquering variability. There I explained some simple ways to reduce the amount of variability that happens in design and construction processes. Experience tells us that we can usually eliminate a lot more unknowns and get typical work processes to settle down a lot more than you might expect. You can read that article here.
That said, this is still building — a world made up of one-off projects, short-term teams, and a whole host of surprises like unexpected weather, unsuitable soils conditions, and the discovery of a protected migratory bird or ancient burial ground on our site. Some variation is sure to be part of every design and construction project.
This leads me to the second part of conquering variability — dealing with the variability that remains. Here are three key practices that we’ve found most effective in dealing with these common challenges.
First, plan and execute work in small batches. Working in small batches does several things to help project work. It allows the work to be connected more tightly together, brings problems to the surface more quickly, and allows the team to respond much faster to unexpected changes. Think of it like this; If you divide the work into small pieces, you will never be far from the start or end of the current piece of work. The conclusion of the current work task provides an opportunity for the team to regroup, lick their wounds, and make a new plan before moving onto the next batch of work.
Next, include buffers that are visible, public, and shared by the entire project team. This one is about building team trust and learning to rely on each other when one member is in a jam. By making collective, visible buffers, you eliminate the need for each project participant to carry their own “secret” buffer to protect themselves against the unknown. Instead of say the roofer, framer, mason, and glazer each carrying their own 10-day schedule contingencies (a total of 40 days) the project can get by with say fewer than 20 days that each member can access if needed. This reduces the total schedule buffer that is required, and provides an opportunity for the team to work together to deal with any unforeseen events. The process provides a safety net while reducing unnecessary contingencies and providing transparency to the team about what is most important for project success.
Finally, make plans and decisions at the last responsible moment. This concept goes contrary to some traditional thinking about planning and decision-making. Yet, once you think about it, it makes perfect sense. Instead of making decisions as soon as possible, we are better off delaying until the moment just before the decision is actually needed. By delaying a decision, we can eliminate the second guessing that happens when we are forced to make decisions based on preliminary or incomplete information. Rather than changing our minds three times and leaving the team with confusion and frustration, we make the decision once with certainty and confidence.
The same concept applies to the creation of project schedules. Greg Howell once put it this way. “The further into the future we attempt to create detailed plans, the more wrong our plans will be.” Rather than creating a CPM schedule with thousands of activities at the start of a project, try focusing on the few important milestones that, if achieved, will guarantee the success of the project. Then, leave the detailed planning to just before that phase of work is set to begin. At that time, you will have more complete information, a more engaged team, and the full attention of the individuals who will actually execute the work. Only then can you make reliable plans that can actually be executed with confidence.
I have no illusions about a design and construction projects running as smoothly as a Toyota assembly line. It’s just a different world with different challenges, Yet, there is a lot we can do to conquer the unique challenges of this environment. Give some thought to reducing some of the variation that you have taken for granted in the past. You can do more than you think. Then design a process that tackles remaining variability head on, with transparency, collaboration, and lean thinking.
For more information about conquering variability, and how to put lean thinking to work in your projects, check out the book, Better Building: Lean Practice for the Project-Driven Organization.
Conquering Variability: A Key to Effective Project Work (Part 2)
By Klaus Lemke
In my previous article, I presented the first part of a process for conquering variability. There I explained some simple ways to reduce the amount of variability that happens in design and construction processes. Experience tells us that we can usually eliminate a lot more unknowns and get typical work processes to settle down a lot more than you might expect. You can read that article here.
That said, this is still building — a world made up of one-off projects, short-term teams, and a whole host of surprises like unexpected weather, unsuitable soils conditions, and the discovery of a protected migratory bird or ancient burial ground on our site. Some variation is sure to be part of every design and construction project.
This leads me to the second part of conquering variability — dealing with the variability that remains. Here are three key practices that we’ve found most effective in dealing with these common challenges.
First, plan and execute work in small batches. Working in small batches does several things to help project work. It allows the work to be connected more tightly together, brings problems to the surface more quickly, and allows the team to respond much faster to unexpected changes. Think of it like this; If you divide the work into small pieces, you will never be far from the start or end of the current piece of work. The conclusion of the current work task provides an opportunity for the team to regroup, lick their wounds, and make a new plan before moving onto the next batch of work.
Next, include buffers that are visible, public, and shared by the entire project team. This one is about building team trust and learning to rely on each other when one member is in a jam. By making collective, visible buffers, you eliminate the need for each project participant to carry their own “secret” buffer to protect themselves against the unknown. Instead of say the roofer, framer, mason, and glazer each carrying their own 10-day schedule contingencies (a total of 40 days) the project can get by with say fewer than 20 days that each member can access if needed. This reduces the total schedule buffer that is required, and provides an opportunity for the team to work together to deal with any unforeseen events. The process provides a safety net while reducing unnecessary contingencies and providing transparency to the team about what is most important for project success.
Finally, make plans and decisions at the last responsible moment. This concept goes contrary to some traditional thinking about planning and decision-making. Yet, once you think about it, it makes perfect sense. Instead of making decisions as soon as possible, we are better off delaying until the moment just before the decision is actually needed. By delaying a decision, we can eliminate the second guessing that happens when we are forced to make decisions based on preliminary or incomplete information. Rather than changing our minds three times and leaving the team with confusion and frustration, we make the decision once with certainty and confidence.
The same concept applies to the creation of project schedules. Greg Howell once put it this way. “The further into the future we attempt to create detailed plans, the more wrong our plans will be.” Rather than creating a CPM schedule with thousands of activities at the start of a project, try focusing on the few important milestones that, if achieved, will guarantee the success of the project. Then, leave the detailed planning to just before that phase of work is set to begin. At that time, you will have more complete information, a more engaged team, and the full attention of the individuals who will actually execute the work. Only then can you make reliable plans that can actually be executed with confidence.
I have no illusions about a design and construction projects running as smoothly as a Toyota assembly line. It’s just a different world with different challenges, Yet, there is a lot we can do to conquer the unique challenges of this environment. Give some thought to reducing some of the variation that you have taken for granted in the past. You can do more than you think. Then design a process that tackles remaining variability head on, with transparency, collaboration, and lean thinking.
For more information about conquering variability, and how to put lean thinking to work in your projects, check out the book, Better Building: Lean Practice for the Project-Driven Organization.
Conquering Variability: A Key to Effective Project Work (Part 2)
By Klaus Lemke
In my previous article, I presented the first part of a process for conquering variability. There I explained some simple ways to reduce the amount of variability that happens in design and construction processes. Experience tells us that we can usually eliminate a lot more unknowns and get typical work processes to settle down a lot more than you might expect. You can read that article here.
That said, this is still building — a world made up of one-off projects, short-term teams, and a whole host of surprises like unexpected weather, unsuitable soils conditions, and the discovery of a protected migratory bird or ancient burial ground on our site. Some variation is sure to be part of every design and construction project.
This leads me to the second part of conquering variability — dealing with the variability that remains. Here are three key practices that we’ve found most effective in dealing with these common challenges.
First, plan and execute work in small batches. Working in small batches does several things to help project work. It allows the work to be connected more tightly together, brings problems to the surface more quickly, and allows the team to respond much faster to unexpected changes. Think of it like this; If you divide the work into small pieces, you will never be far from the start or end of the current piece of work. The conclusion of the current work task provides an opportunity for the team to regroup, lick their wounds, and make a new plan before moving onto the next batch of work.
Next, include buffers that are visible, public, and shared by the entire project team. This one is about building team trust and learning to rely on each other when one member is in a jam. By making collective, visible buffers, you eliminate the need for each project participant to carry their own “secret” buffer to protect themselves against the unknown. Instead of say the roofer, framer, mason, and glazer each carrying their own 10-day schedule contingencies (a total of 40 days) the project can get by with say fewer than 20 days that each member can access if needed. This reduces the total schedule buffer that is required, and provides an opportunity for the team to work together to deal with any unforeseen events. The process provides a safety net while reducing unnecessary contingencies and providing transparency to the team about what is most important for project success.
Finally, make plans and decisions at the last responsible moment. This concept goes contrary to some traditional thinking about planning and decision-making. Yet, once you think about it, it makes perfect sense. Instead of making decisions as soon as possible, we are better off delaying until the moment just before the decision is actually needed. By delaying a decision, we can eliminate the second guessing that happens when we are forced to make decisions based on preliminary or incomplete information. Rather than changing our minds three times and leaving the team with confusion and frustration, we make the decision once with certainty and confidence.
The same concept applies to the creation of project schedules. Greg Howell once put it this way. “The further into the future we attempt to create detailed plans, the more wrong our plans will be.” Rather than creating a CPM schedule with thousands of activities at the start of a project, try focusing on the few important milestones that, if achieved, will guarantee the success of the project. Then, leave the detailed planning to just before that phase of work is set to begin. At that time, you will have more complete information, a more engaged team, and the full attention of the individuals who will actually execute the work. Only then can you make reliable plans that can actually be executed with confidence.
I have no illusions about a design and construction projects running as smoothly as a Toyota assembly line. It’s just a different world with different challenges, Yet, there is a lot we can do to conquer the unique challenges of this environment. Give some thought to reducing some of the variation that you have taken for granted in the past. You can do more than you think. Then design a process that tackles remaining variability head on, with transparency, collaboration, and lean thinking.
For more information about conquering variability, and how to put lean thinking to work in your projects, check out the book, Better Building: Lean Practice for the Project-Driven Organization.
Conquering Variability: A Key to Effective Project Work (Part 2)
In part 2, Klaus Lemke shares insights on using lean thinking to reduce and manage variability in construction, overcoming challenges unique to project work.
Conquering Variability: A Key to Effective Project Work (Part 2)
By Klaus Lemke
In my previous article, I presented the first part of a process for conquering variability. There I explained some simple ways to reduce the amount of variability that happens in design and construction processes. Experience tells us that we can usually eliminate a lot more unknowns and get typical work processes to settle down a lot more than you might expect. You can read that article here.
That said, this is still building — a world made up of one-off projects, short-term teams, and a whole host of surprises like unexpected weather, unsuitable soils conditions, and the discovery of a protected migratory bird or ancient burial ground on our site. Some variation is sure to be part of every design and construction project.
This leads me to the second part of conquering variability — dealing with the variability that remains. Here are three key practices that we’ve found most effective in dealing with these common challenges.
First, plan and execute work in small batches. Working in small batches does several things to help project work. It allows the work to be connected more tightly together, brings problems to the surface more quickly, and allows the team to respond much faster to unexpected changes. Think of it like this; If you divide the work into small pieces, you will never be far from the start or end of the current piece of work. The conclusion of the current work task provides an opportunity for the team to regroup, lick their wounds, and make a new plan before moving onto the next batch of work.
Next, include buffers that are visible, public, and shared by the entire project team. This one is about building team trust and learning to rely on each other when one member is in a jam. By making collective, visible buffers, you eliminate the need for each project participant to carry their own “secret” buffer to protect themselves against the unknown. Instead of say the roofer, framer, mason, and glazer each carrying their own 10-day schedule contingencies (a total of 40 days) the project can get by with say fewer than 20 days that each member can access if needed. This reduces the total schedule buffer that is required, and provides an opportunity for the team to work together to deal with any unforeseen events. The process provides a safety net while reducing unnecessary contingencies and providing transparency to the team about what is most important for project success.
Finally, make plans and decisions at the last responsible moment. This concept goes contrary to some traditional thinking about planning and decision-making. Yet, once you think about it, it makes perfect sense. Instead of making decisions as soon as possible, we are better off delaying until the moment just before the decision is actually needed. By delaying a decision, we can eliminate the second guessing that happens when we are forced to make decisions based on preliminary or incomplete information. Rather than changing our minds three times and leaving the team with confusion and frustration, we make the decision once with certainty and confidence.
The same concept applies to the creation of project schedules. Greg Howell once put it this way. “The further into the future we attempt to create detailed plans, the more wrong our plans will be.” Rather than creating a CPM schedule with thousands of activities at the start of a project, try focusing on the few important milestones that, if achieved, will guarantee the success of the project. Then, leave the detailed planning to just before that phase of work is set to begin. At that time, you will have more complete information, a more engaged team, and the full attention of the individuals who will actually execute the work. Only then can you make reliable plans that can actually be executed with confidence.
I have no illusions about a design and construction projects running as smoothly as a Toyota assembly line. It’s just a different world with different challenges, Yet, there is a lot we can do to conquer the unique challenges of this environment. Give some thought to reducing some of the variation that you have taken for granted in the past. You can do more than you think. Then design a process that tackles remaining variability head on, with transparency, collaboration, and lean thinking.
For more information about conquering variability, and how to put lean thinking to work in your projects, check out the book, Better Building: Lean Practice for the Project-Driven Organization.
Conquering Variability: A Key to Effective Project Work (Part 2)
In part 2, Klaus Lemke shares insights on using lean thinking to reduce and manage variability in construction, overcoming challenges unique to project work.
Conquering Variability: A Key to Effective Project Work (Part 2)
By Klaus Lemke
In my previous article, I presented the first part of a process for conquering variability. There I explained some simple ways to reduce the amount of variability that happens in design and construction processes. Experience tells us that we can usually eliminate a lot more unknowns and get typical work processes to settle down a lot more than you might expect. You can read that article here.
That said, this is still building — a world made up of one-off projects, short-term teams, and a whole host of surprises like unexpected weather, unsuitable soils conditions, and the discovery of a protected migratory bird or ancient burial ground on our site. Some variation is sure to be part of every design and construction project.
This leads me to the second part of conquering variability — dealing with the variability that remains. Here are three key practices that we’ve found most effective in dealing with these common challenges.
First, plan and execute work in small batches. Working in small batches does several things to help project work. It allows the work to be connected more tightly together, brings problems to the surface more quickly, and allows the team to respond much faster to unexpected changes. Think of it like this; If you divide the work into small pieces, you will never be far from the start or end of the current piece of work. The conclusion of the current work task provides an opportunity for the team to regroup, lick their wounds, and make a new plan before moving onto the next batch of work.
Next, include buffers that are visible, public, and shared by the entire project team. This one is about building team trust and learning to rely on each other when one member is in a jam. By making collective, visible buffers, you eliminate the need for each project participant to carry their own “secret” buffer to protect themselves against the unknown. Instead of say the roofer, framer, mason, and glazer each carrying their own 10-day schedule contingencies (a total of 40 days) the project can get by with say fewer than 20 days that each member can access if needed. This reduces the total schedule buffer that is required, and provides an opportunity for the team to work together to deal with any unforeseen events. The process provides a safety net while reducing unnecessary contingencies and providing transparency to the team about what is most important for project success.
Finally, make plans and decisions at the last responsible moment. This concept goes contrary to some traditional thinking about planning and decision-making. Yet, once you think about it, it makes perfect sense. Instead of making decisions as soon as possible, we are better off delaying until the moment just before the decision is actually needed. By delaying a decision, we can eliminate the second guessing that happens when we are forced to make decisions based on preliminary or incomplete information. Rather than changing our minds three times and leaving the team with confusion and frustration, we make the decision once with certainty and confidence.
The same concept applies to the creation of project schedules. Greg Howell once put it this way. “The further into the future we attempt to create detailed plans, the more wrong our plans will be.” Rather than creating a CPM schedule with thousands of activities at the start of a project, try focusing on the few important milestones that, if achieved, will guarantee the success of the project. Then, leave the detailed planning to just before that phase of work is set to begin. At that time, you will have more complete information, a more engaged team, and the full attention of the individuals who will actually execute the work. Only then can you make reliable plans that can actually be executed with confidence.
I have no illusions about a design and construction projects running as smoothly as a Toyota assembly line. It’s just a different world with different challenges, Yet, there is a lot we can do to conquer the unique challenges of this environment. Give some thought to reducing some of the variation that you have taken for granted in the past. You can do more than you think. Then design a process that tackles remaining variability head on, with transparency, collaboration, and lean thinking.
For more information about conquering variability, and how to put lean thinking to work in your projects, check out the book, Better Building: Lean Practice for the Project-Driven Organization.
Conquering Variability: A Key to Effective Project Work (Part 2)
By Klaus Lemke
In my previous article, I presented the first part of a process for conquering variability. There I explained some simple ways to reduce the amount of variability that happens in design and construction processes. Experience tells us that we can usually eliminate a lot more unknowns and get typical work processes to settle down a lot more than you might expect. You can read that article here.
That said, this is still building — a world made up of one-off projects, short-term teams, and a whole host of surprises like unexpected weather, unsuitable soils conditions, and the discovery of a protected migratory bird or ancient burial ground on our site. Some variation is sure to be part of every design and construction project.
This leads me to the second part of conquering variability — dealing with the variability that remains. Here are three key practices that we’ve found most effective in dealing with these common challenges.
First, plan and execute work in small batches. Working in small batches does several things to help project work. It allows the work to be connected more tightly together, brings problems to the surface more quickly, and allows the team to respond much faster to unexpected changes. Think of it like this; If you divide the work into small pieces, you will never be far from the start or end of the current piece of work. The conclusion of the current work task provides an opportunity for the team to regroup, lick their wounds, and make a new plan before moving onto the next batch of work.
Next, include buffers that are visible, public, and shared by the entire project team. This one is about building team trust and learning to rely on each other when one member is in a jam. By making collective, visible buffers, you eliminate the need for each project participant to carry their own “secret” buffer to protect themselves against the unknown. Instead of say the roofer, framer, mason, and glazer each carrying their own 10-day schedule contingencies (a total of 40 days) the project can get by with say fewer than 20 days that each member can access if needed. This reduces the total schedule buffer that is required, and provides an opportunity for the team to work together to deal with any unforeseen events. The process provides a safety net while reducing unnecessary contingencies and providing transparency to the team about what is most important for project success.
Finally, make plans and decisions at the last responsible moment. This concept goes contrary to some traditional thinking about planning and decision-making. Yet, once you think about it, it makes perfect sense. Instead of making decisions as soon as possible, we are better off delaying until the moment just before the decision is actually needed. By delaying a decision, we can eliminate the second guessing that happens when we are forced to make decisions based on preliminary or incomplete information. Rather than changing our minds three times and leaving the team with confusion and frustration, we make the decision once with certainty and confidence.
The same concept applies to the creation of project schedules. Greg Howell once put it this way. “The further into the future we attempt to create detailed plans, the more wrong our plans will be.” Rather than creating a CPM schedule with thousands of activities at the start of a project, try focusing on the few important milestones that, if achieved, will guarantee the success of the project. Then, leave the detailed planning to just before that phase of work is set to begin. At that time, you will have more complete information, a more engaged team, and the full attention of the individuals who will actually execute the work. Only then can you make reliable plans that can actually be executed with confidence.
I have no illusions about a design and construction projects running as smoothly as a Toyota assembly line. It’s just a different world with different challenges, Yet, there is a lot we can do to conquer the unique challenges of this environment. Give some thought to reducing some of the variation that you have taken for granted in the past. You can do more than you think. Then design a process that tackles remaining variability head on, with transparency, collaboration, and lean thinking.
For more information about conquering variability, and how to put lean thinking to work in your projects, check out the book, Better Building: Lean Practice for the Project-Driven Organization.
Conquering Variability: A Key to Effective Project Work (Part 2)
By Klaus Lemke
In my previous article, I presented the first part of a process for conquering variability. There I explained some simple ways to reduce the amount of variability that happens in design and construction processes. Experience tells us that we can usually eliminate a lot more unknowns and get typical work processes to settle down a lot more than you might expect. You can read that article here.
That said, this is still building — a world made up of one-off projects, short-term teams, and a whole host of surprises like unexpected weather, unsuitable soils conditions, and the discovery of a protected migratory bird or ancient burial ground on our site. Some variation is sure to be part of every design and construction project.
This leads me to the second part of conquering variability — dealing with the variability that remains. Here are three key practices that we’ve found most effective in dealing with these common challenges.
First, plan and execute work in small batches. Working in small batches does several things to help project work. It allows the work to be connected more tightly together, brings problems to the surface more quickly, and allows the team to respond much faster to unexpected changes. Think of it like this; If you divide the work into small pieces, you will never be far from the start or end of the current piece of work. The conclusion of the current work task provides an opportunity for the team to regroup, lick their wounds, and make a new plan before moving onto the next batch of work.
Next, include buffers that are visible, public, and shared by the entire project team. This one is about building team trust and learning to rely on each other when one member is in a jam. By making collective, visible buffers, you eliminate the need for each project participant to carry their own “secret” buffer to protect themselves against the unknown. Instead of say the roofer, framer, mason, and glazer each carrying their own 10-day schedule contingencies (a total of 40 days) the project can get by with say fewer than 20 days that each member can access if needed. This reduces the total schedule buffer that is required, and provides an opportunity for the team to work together to deal with any unforeseen events. The process provides a safety net while reducing unnecessary contingencies and providing transparency to the team about what is most important for project success.
Finally, make plans and decisions at the last responsible moment. This concept goes contrary to some traditional thinking about planning and decision-making. Yet, once you think about it, it makes perfect sense. Instead of making decisions as soon as possible, we are better off delaying until the moment just before the decision is actually needed. By delaying a decision, we can eliminate the second guessing that happens when we are forced to make decisions based on preliminary or incomplete information. Rather than changing our minds three times and leaving the team with confusion and frustration, we make the decision once with certainty and confidence.
The same concept applies to the creation of project schedules. Greg Howell once put it this way. “The further into the future we attempt to create detailed plans, the more wrong our plans will be.” Rather than creating a CPM schedule with thousands of activities at the start of a project, try focusing on the few important milestones that, if achieved, will guarantee the success of the project. Then, leave the detailed planning to just before that phase of work is set to begin. At that time, you will have more complete information, a more engaged team, and the full attention of the individuals who will actually execute the work. Only then can you make reliable plans that can actually be executed with confidence.
I have no illusions about a design and construction projects running as smoothly as a Toyota assembly line. It’s just a different world with different challenges, Yet, there is a lot we can do to conquer the unique challenges of this environment. Give some thought to reducing some of the variation that you have taken for granted in the past. You can do more than you think. Then design a process that tackles remaining variability head on, with transparency, collaboration, and lean thinking.
For more information about conquering variability, and how to put lean thinking to work in your projects, check out the book, Better Building: Lean Practice for the Project-Driven Organization.
Conquering Variability: A Key to Effective Project Work (Part 2)
By Klaus Lemke
In my previous article, I presented the first part of a process for conquering variability. There I explained some simple ways to reduce the amount of variability that happens in design and construction processes. Experience tells us that we can usually eliminate a lot more unknowns and get typical work processes to settle down a lot more than you might expect. You can read that article here.
That said, this is still building — a world made up of one-off projects, short-term teams, and a whole host of surprises like unexpected weather, unsuitable soils conditions, and the discovery of a protected migratory bird or ancient burial ground on our site. Some variation is sure to be part of every design and construction project.
This leads me to the second part of conquering variability — dealing with the variability that remains. Here are three key practices that we’ve found most effective in dealing with these common challenges.
First, plan and execute work in small batches. Working in small batches does several things to help project work. It allows the work to be connected more tightly together, brings problems to the surface more quickly, and allows the team to respond much faster to unexpected changes. Think of it like this; If you divide the work into small pieces, you will never be far from the start or end of the current piece of work. The conclusion of the current work task provides an opportunity for the team to regroup, lick their wounds, and make a new plan before moving onto the next batch of work.
Next, include buffers that are visible, public, and shared by the entire project team. This one is about building team trust and learning to rely on each other when one member is in a jam. By making collective, visible buffers, you eliminate the need for each project participant to carry their own “secret” buffer to protect themselves against the unknown. Instead of say the roofer, framer, mason, and glazer each carrying their own 10-day schedule contingencies (a total of 40 days) the project can get by with say fewer than 20 days that each member can access if needed. This reduces the total schedule buffer that is required, and provides an opportunity for the team to work together to deal with any unforeseen events. The process provides a safety net while reducing unnecessary contingencies and providing transparency to the team about what is most important for project success.
Finally, make plans and decisions at the last responsible moment. This concept goes contrary to some traditional thinking about planning and decision-making. Yet, once you think about it, it makes perfect sense. Instead of making decisions as soon as possible, we are better off delaying until the moment just before the decision is actually needed. By delaying a decision, we can eliminate the second guessing that happens when we are forced to make decisions based on preliminary or incomplete information. Rather than changing our minds three times and leaving the team with confusion and frustration, we make the decision once with certainty and confidence.
The same concept applies to the creation of project schedules. Greg Howell once put it this way. “The further into the future we attempt to create detailed plans, the more wrong our plans will be.” Rather than creating a CPM schedule with thousands of activities at the start of a project, try focusing on the few important milestones that, if achieved, will guarantee the success of the project. Then, leave the detailed planning to just before that phase of work is set to begin. At that time, you will have more complete information, a more engaged team, and the full attention of the individuals who will actually execute the work. Only then can you make reliable plans that can actually be executed with confidence.
I have no illusions about a design and construction projects running as smoothly as a Toyota assembly line. It’s just a different world with different challenges, Yet, there is a lot we can do to conquer the unique challenges of this environment. Give some thought to reducing some of the variation that you have taken for granted in the past. You can do more than you think. Then design a process that tackles remaining variability head on, with transparency, collaboration, and lean thinking.
For more information about conquering variability, and how to put lean thinking to work in your projects, check out the book, Better Building: Lean Practice for the Project-Driven Organization.