The Two Great Wastes in Organizations
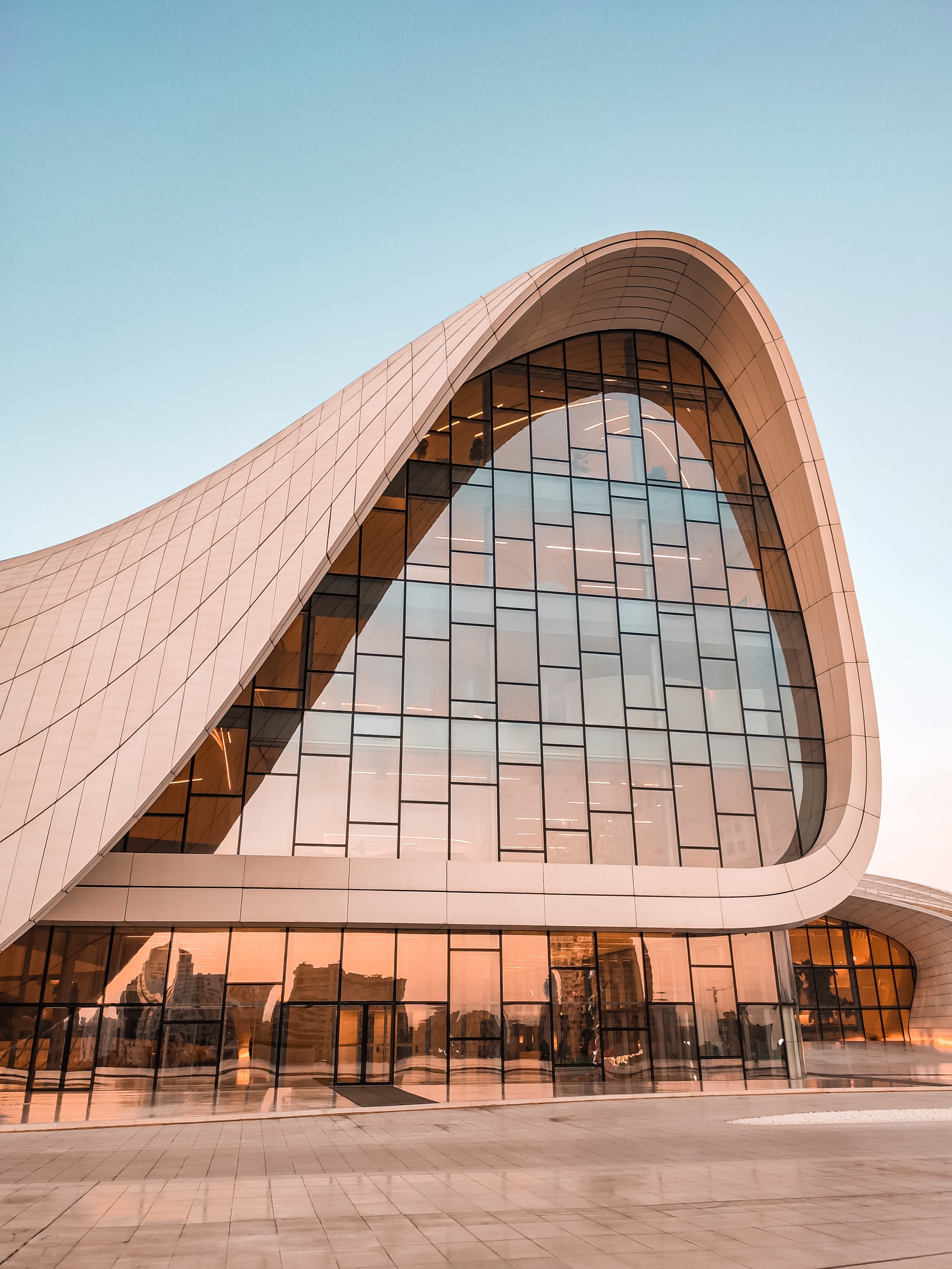
The Two Great Wastes in Organizations
The Toyota Production System is so successful that people look for ways to apply the lean production ideas and methods in organization settings. One of those ways is the force-fitting of Engineer Taiichi Ohno’s seven wastes to organizations and projects. While organizations and projects manipulate materiel, they are better characterized by their actions of accomplishing something together — coordinating action, learning, and innovating. The seven wastes don’t address those actions. Attempts to add to the seven wastes have to date broken the Ohno taxonomy. The authors propose a novel set of distinctions on the principal sources of waste in organizational settings.
The Two Great Wastes in Organizations
The Toyota Production System is so successful that people look for ways to apply the lean production ideas and methods in organization settings. One of those ways is the force-fitting of Engineer Taiichi Ohno’s seven wastes to organizations and projects. While organizations and projects manipulate materiel, they are better characterized by their actions of accomplishing something together — coordinating action, learning, and innovating. The seven wastes don’t address those actions. Attempts to add to the seven wastes have to date broken the Ohno taxonomy. The authors propose a novel set of distinctions on the principal sources of waste in organizational settings.
The Two Great Wastes in Organizations
The Toyota Production System is so successful that people look for ways to apply the lean production ideas and methods in organization settings. One of those ways is the force-fitting of Engineer Taiichi Ohno’s seven wastes to organizations and projects. While organizations and projects manipulate materiel, they are better characterized by their actions of accomplishing something together — coordinating action, learning, and innovating. The seven wastes don’t address those actions. Attempts to add to the seven wastes have to date broken the Ohno taxonomy. The authors propose a novel set of distinctions on the principal sources of waste in organizational settings.
The Two Great Wastes in Organizations
The Toyota Production System is so successful that people look for ways to apply the lean production ideas and methods in organization settings. One of those ways is the force-fitting of Engineer Taiichi Ohno’s seven wastes to organizations and projects. While organizations and projects manipulate materiel, they are better characterized by their actions of accomplishing something together — coordinating action, learning, and innovating. The seven wastes don’t address those actions. Attempts to add to the seven wastes have to date broken the Ohno taxonomy. The authors propose a novel set of distinctions on the principal sources of waste in organizational settings.
The Two Great Wastes in Organizations
The Toyota Production System is so successful that people look for ways to apply the lean production ideas and methods in organization settings.
The Two Great Wastes in Organizations
The Toyota Production System is so successful that people look for ways to apply the lean production ideas and methods in organization settings. One of those ways is the force-fitting of Engineer Taiichi Ohno’s seven wastes to organizations and projects. While organizations and projects manipulate materiel, they are better characterized by their actions of accomplishing something together — coordinating action, learning, and innovating. The seven wastes don’t address those actions. Attempts to add to the seven wastes have to date broken the Ohno taxonomy. The authors propose a novel set of distinctions on the principal sources of waste in organizational settings.
The Two Great Wastes in Organizations
The Toyota Production System is so successful that people look for ways to apply the lean production ideas and methods in organization settings.
The Two Great Wastes in Organizations
The Toyota Production System is so successful that people look for ways to apply the lean production ideas and methods in organization settings. One of those ways is the force-fitting of Engineer Taiichi Ohno’s seven wastes to organizations and projects. While organizations and projects manipulate materiel, they are better characterized by their actions of accomplishing something together — coordinating action, learning, and innovating. The seven wastes don’t address those actions. Attempts to add to the seven wastes have to date broken the Ohno taxonomy. The authors propose a novel set of distinctions on the principal sources of waste in organizational settings.
The Two Great Wastes in Organizations
The Toyota Production System is so successful that people look for ways to apply the lean production ideas and methods in organization settings. One of those ways is the force-fitting of Engineer Taiichi Ohno’s seven wastes to organizations and projects. While organizations and projects manipulate materiel, they are better characterized by their actions of accomplishing something together — coordinating action, learning, and innovating. The seven wastes don’t address those actions. Attempts to add to the seven wastes have to date broken the Ohno taxonomy. The authors propose a novel set of distinctions on the principal sources of waste in organizational settings.
The Two Great Wastes in Organizations
The Toyota Production System is so successful that people look for ways to apply the lean production ideas and methods in organization settings. One of those ways is the force-fitting of Engineer Taiichi Ohno’s seven wastes to organizations and projects. While organizations and projects manipulate materiel, they are better characterized by their actions of accomplishing something together — coordinating action, learning, and innovating. The seven wastes don’t address those actions. Attempts to add to the seven wastes have to date broken the Ohno taxonomy. The authors propose a novel set of distinctions on the principal sources of waste in organizational settings.
The Two Great Wastes in Organizations
The Toyota Production System is so successful that people look for ways to apply the lean production ideas and methods in organization settings. One of those ways is the force-fitting of Engineer Taiichi Ohno’s seven wastes to organizations and projects. While organizations and projects manipulate materiel, they are better characterized by their actions of accomplishing something together — coordinating action, learning, and innovating. The seven wastes don’t address those actions. Attempts to add to the seven wastes have to date broken the Ohno taxonomy. The authors propose a novel set of distinctions on the principal sources of waste in organizational settings.